- Publication Date:
- 21 May 2021 г.
A hydraulic pump is one of the main components of any hydraulic system. It is designed to pump pressurized liquids through hydraulic systems. Hydraulic pumps boast high performance (except for manual models), durability, and are widely used in machinery.
Main features of hydraulic pumps
Main performance characteristics of hydraulic pumps to be considered when selecting a suitable type of unit and a specific model:
- displacement — volume of liquid displaced by the hydraulic pump during 1 shaft rotation by 360°;
- range of permissible operating pressures;
- shaft rotation rpm rated by the manufacturer;
- overall dimensions;
- permissible viscosity of the working medium and its purity class;
- maintainability;
- brand, cost;
- economic feasibility of buying a particular model.
Types of hydraulic pumps
By type of main functional elements, hydraulic pumps are divided into piston, gear, and vane pumps, which, in turn, are further divided into subtypes.
Piston pumps
Subtypes of piston hydraulic pumps:
- Manual pumps. These can be single- and double-acting. Usually, these are used as a backup power source, including emergency. Can be used to supply power to hydraulic servomotors. Manual piston hydraulic pumps are suitable for hydraulic systems with pressures not exceeding 15 MPa. Their pros are simple designs, reliability. Unfortunately, their pumping capacity is low.
- Axial piston pumps are high-speed. They are equipped with axially located cylinders. This is the most popular type of hydraulic units. These are characterized by high specific output and efficiency, simple design. The disadvantage is probable pressure surges. Compared to their analogs, axial piston models are more expensive.
- Radial piston pumps. These devices have an eccentric shaft or rotor. They are used in hydraulic systems with high pressures (40 MPa and higher). Radial piston hydraulic pumps come in an uncomplicated design, their axial dimension is small. They are reliable, can create pressure up to 100 MPa. The cons include unstable working pressures, low shaft rpm.
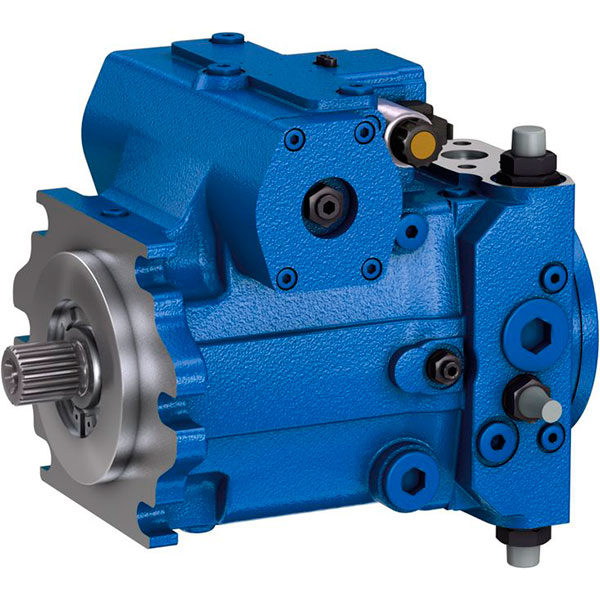
Gear pumps
The main functional elements of these hydraulic pumps are two rotating gears. Models differ in the way of engagement — external or internal. Gear hydraulic pumps are suitable for hydraulic systems with pressures up to 20 MPa. The main areas of use are agricultural machinery and highway road construction equipment. Such units effectively energize auxiliary mechanisms in multi-component hydraulic systems.
The pros of gear pumps are:
- simple design;
- space-saving dimensions;
- significant rotational speed: gear models with internal engagement reach the speed of up to 5,000 rpm, those with external engagement — up to 4,000 rpm.
- low weight;
- low cost.
The cons include low working pressure and efficiency, a relatively short service life.
Gerotor models (another type of gear hydraulic pumps) are used in low-pressure systems. Rotational speed is not higher than 1,500 rpm. These units are low-noise.
Vane pumps
Vane hydraulic pumps have radially placed plates that perform reciprocating movements when the rotor rotates. Another name for the plates is paddles, so such units are also called paddle pumps. A distinction is made between single-acting and double-acting models.
The pros of single-acting vane pumps are:
- pressure stability;
- displacement control;
- relatively low cost.
The cons of these models are: complicated maintenance, low pressure values — up to 7 MPa.
Double-acting units differ from their single-acting counterparts by the presence of two discharge and suction zones, which makes it possible to use them in systems with higher pressure — up to 21 MPa.